Swiss Medtech calls for amendment of the national medical devices ordinance
How is the Swiss medtech industry doing just six months after being downgraded to a third country? The answer: the sector is in a good position to export medical devices in accordance with the new EU regulations. The situation with imports is alarming. With the home-made import hurdles, Switzerland is endangering the health care of its own population. Swiss Medtech is therefore urgently calling for an amendment to the national Medical Devices Ordinance.
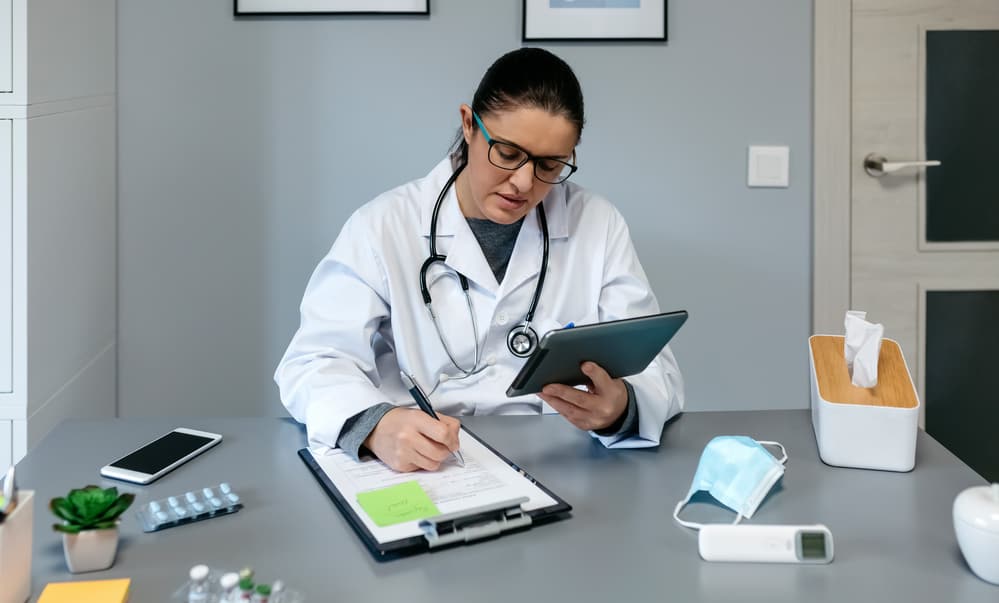
This year's Swiss Medtech conference on medical device regulation on 19 October was dominated by the new reality Third countryThe Swiss medical technology industry has been in a state of deadlock with the European Union (EU) - its most important trading partner - since May of this year. What are the consequences of the blockade with the EU on the Swiss medical technology industry, which has so far been marked by success? What are the acute problems and how could they be solved? At the conference, over 500 industry representatives explored these questions.
Exports: the industry has come to terms
According to Swiss Medtech, the industry has not yet Third country The company has largely anticipated this and has spent two years preparing itself with great commitment to meet the additional requirements for the seamless export of its goods to the EU. These essentially include the appointment of an authorised representative in the EU area, who assumes the manufacturer's tasks and joint and several product liability on behalf of the manufacturer, as well as the re-labelling of the products. Today, almost all companies are set up accordingly. The legal situation is clear: anyone wishing to export MDR¹ products to the EU must comply with the third-country requirements. On the other hand, there is still legal uncertainty with regard to medical devices with existing certificates (so-called MDD² products or old-law products). May they benefit from the transition period until the end of 2024 or not? "The EU says no, Switzerland says yes," the industry association said. Each company must make its own risk assessment in this legal limbo.
Import: Alarming situation - patient care is at risk
With the entry into force of the national Medical Devices Ordinance (MepV) on 26 May 2021, the Federal Council has set high import barriers for foreign manufacturers. In doing so, Switzerland is not only harming the domestic medtech industry, but is also endangering the healthcare of its own population. According to Swiss Medtech, industry surveys show that one in eight of the medical products currently used in Switzerland will no longer be available in the future. The reason: not all foreign manufacturers are prepared to meet additional requirements solely for the small Swiss market. "At the moment, we are aware of individual examples of supply stoppages. From the second half of next year, there will be broadly noticeable gaps in supply," Daniel Delfosse, Head of Regulatory Affairs at Swiss Medtech, is convinced.
Already in spring this year, the association, together with other health stakeholders, drew attention to the alarming situation in an open letter to the Federal Council. Without success: The MepV was put into force with high import hurdles.
The association is aware that the Federal Council does not have the MRA³ update and thus the key to free mutual trade in goods in its own hands, but that the EU must also be prepared to do so. "It is all the more important that the Federal Council makes the rules of import, which it can set unilaterally independently of the EU by means of the MepV, for the benefit of Switzerland. That is not the case today," says Delfosse. With the MepV, Switzerland has further tightened the law adopted by the EU (MDR) (Swiss Finish). "The bill does not work in reality. We call for an urgent amendment. With a few adjustments to the ordinance, the looming supply problem could be massively defused. The Swiss government alone has this in its hands," says Delfosse.
Future: Putting relations with the EU on a sound footing
In addition to the short-term negative consequences, the long-term damage to Switzerland as an attractive medtech location should not be forgotten. "Many decision-makers do not seem to be aware of how much the blockade with the EU has already damaged and will continue to damage Switzerland's attractiveness as a business and research location. The association will therefore continue to work with unwavering commitment with partners and in alliances to ensure that Switzerland's relationship with the EU is placed on a solid and lasting footing," says Beat Vonlanthen, President of Swiss Medtech.
Source: Swiss Medtech
Review of the European Medtech-Staccato
May 26, 2021 was a cut-off date for the medtech industry: The new European Medical Device Regulation (MDR) replaced the old EU Directives (MDD). The national Medical Device Regulation (MepV) came into force. The Federal Council broke off negotiations with the EU on the Institutional Framework Agreement, which abruptly lost the opportunity to update the agreement on the free bilateral trade of medical devices (³Mutual Recognition Agreement, MRA) in a timely manner. The lack of an update of the MRA relegated the Swiss medtech sector to third country status. The EU Commission announced that Swiss certificates would no longer be recognised in the EU with immediate effect, and that products with existing certificates issued by a body in the EU would not be able to benefit from the transition period until May 2024.