L'informatique de production : la voie vers une production parfaite
Quelle commande produisez-vous actuellement ? Où en est la commande ? Et de quel outil avez-vous besoin ensuite ? S'il est encore relativement facile de répondre à ces trois questions, il en va tout autrement ici : Quel est le potentiel encore présent dans vos installations - et pas au feeling ? Connaissez-vous les causes de panne les plus fréquentes - et ce, sur le bout des doigts ? Quelles sont vos possibilités d'évitement en cas de panne - et vite, vite ? Dans l'environnement de marché actuel, il est essentiel d'obtenir des réponses rapides. Dans cet article, vous apprendrez comment devenir pertinent et atteindre les objectifs d'une production parfaite.
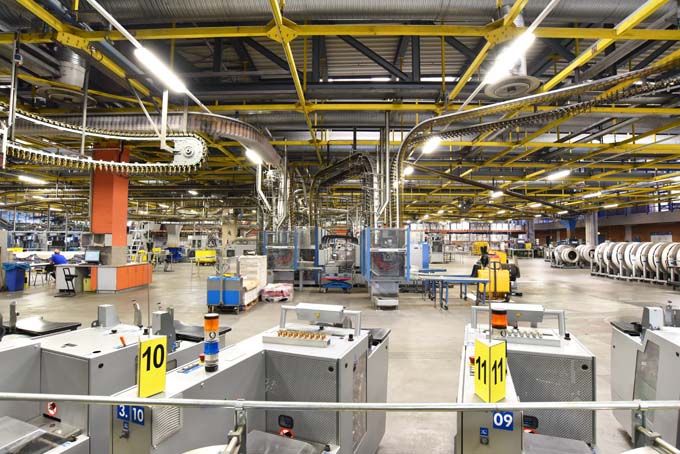
Pour avoir toujours la bonne réponse sous la main, vous avez d'abord besoin d'une chose dans la production : Transparence - et ce, en appuyant sur un bouton. En collaboration avec la Réactivité elle fait partie des valeurs cibles primaires qu'une entreprise doit poursuivre. La transparence et la réactivité sont à leur tour des conditions préalables pour Rentabilité - la troisième valeur cible du triangle magique de la production parfaite. En effet, ce n'est que lorsque les processus d'une entreprise de production peuvent être régulés par des circuits de régulation rapides que la rentabilité peut être augmentée et que la compétitivité peut être assurée.
Petite cause, grand effet
Un exemple pratique illustre les relations : un minuscule copeau de métal dans l'huile peut entraîner la défaillance d'une pompe à huile. En conséquence, le roulement est endommagé et provoque l'arrêt complet d'une machine. La machine s'arrête, la commande n'est pas terminée à temps et, dans le pire des cas, le dépassement de la date de livraison entraîne une pénalité. C'est ainsi que les choses se passent encore dans de nombreuses usines.
Dans une production transparente, réactive et économique, le scénario serait différent. Le chef d'équipe n'aurait qu'à jeter un coup d'œil à son IT de production pour voir sur quelle machine il peut se rabattre en cas de panne (transparence). Grâce au soutien du système, il pourrait replanifier les commandes en quelques clics (réactivité) et respecter le délai de livraison (rentabilité). Il est même possible de faire mieux : si les possibilités offertes par l'informatique de production moderne étaient utilisées, la machine ne serait même pas tombée en panne. Predictive Maintenance ou maintenance prédictive est le mot magique. Les données des machines et des processus saisies sans faille pourraient être analysées avec précision afin d'entretenir les machines de manière proactive et d'éviter les arrêts imprévus.
Quatre éléments constitutifs d'une production parfaite
Le cas décrit montre que l'objectif d'une production parfaite est inévitablement lié à la numérisation. Mais pour réussir la transformation en une usine intelligente, il ne suffit pas d'installer les équipements de production les plus modernes et un Manufacturing Execution System (MES). Il faut également créer les conditions-cadres permettant d'utiliser efficacement l'informatique de fabrication. Une approche globale se consacre donc aux aspects suivants :
- Gestion de la chaîne de valeur 4.0
- Flux de valeurs allégés
- Des fonctions de soutien allégées
- Amélioration durable des processus
Ces quatre modules ont fait leurs preuves en permettant aux entreprises d'atteindre progressivement une production parfaite. Ils visent à identifier les points faibles et à les éviter à l'avenir.
Module 1 : Gestion des flux de valeurs 4.0
Le premier module comprend essentiellement l'analyse du flux de valeur 4.0 et la conception du flux de valeur. Il sert donc à reprendre les processus, à les analyser et à les reconcevoir. Outre le processus de fabrication et le flux de matières, une attention particulière est accordée aux flux d'informations et aux processus de planification. En effet, ils contrôlent les processus de fabrication, où chaque minute compte. Les conclusions de l'analyse à 360 degrés sont représentées dans un diagramme de flux de valeur. Afin de pouvoir évaluer rapidement les informations ainsi illustrées, un diagramme des temps de passage est établi et le rendement du processus est calculé comme mesure de la rentabilité de l'ensemble du processus. Pour le domaine des flux d'information et des processus de planification, on détermine par exemple le nombre d'outils utilisés et le degré de numérisation.
Les faits concernant les processus dans la production et l'environnement proche de la production sont désormais clairs. Il est possible de répondre aux questions concernant le processus de fabrication, le flux d'informations, le processus de planification et les outils (informatiques) utilisés et d'en déduire les prochaines étapes : une conception du flux de valeur avec un concept théorique ainsi qu'une feuille de route pour mettre en œuvre le concept théorique.
Module 2 : Flux de valeurs allégés
Le deuxième module vise à établir des processus de production allégés, c'est-à-dire à mettre en œuvre de manière cohérente le concept théorique élaboré dans le premier module. Cela va de pair avec l'élimination du gaspillage. Parmi les sept types de gaspillage les plus courants, en référence à Taiichi Ohno, ancien directeur de la production chez Toyota et fondateur de la production allégée, on trouve : la surproduction, les temps d'attente, le transport, l'usinage inefficace, les stocks, les mouvements superflus et les erreurs. On peut y ajouter le manque d'implication et de motivation des collaborateurs ainsi que le gaspillage dû aux interfaces d'information. En effet, pour une mise en œuvre réussie de flux de valeurs allégés, l'implication active des collaborateurs est essentielle.
Module 3 : Fonctions de soutien allégées
Le troisième module s'intéresse aux fonctions de soutien proches de la production, c'est-à-dire à la planification générale et détaillée et à leur intégration dans les processus de fabrication. Un exemple frappant est l'optimisation de la planification : souvent, la production est planifiée sommairement dans le système ERP sur des semaines calendaires. La planification fine sur les postes de travail et les machines se fait ensuite au jour ou à l'équipe près sur le tableau de planification dans le bureau du contremaître ou dans Excel. Il est évident que la transparence, mais aussi la capacité de réaction au sens de boucles de régulation rapides, en sont totalement absentes. Comme les capacités réelles et les retards de commande ne sont pas pris en compte, les ordres de fabrication ou les délais sont tout simplement irréalisables. Un outil de planification intégré dans un Manufacturing Execution System permet de remédier à cette situation. Il aide à établir la transparence et la capacité de réaction. En effet, dans une production parfaite, ce ne sont pas seulement les matériaux qui doivent circuler, mais aussi les informations.
Module 4 : Amélioration durable des processus
Dès que les processus sont allégés et numérisés, il s'agit, dans la quatrième composante, d'implémenter durablement les changements dans l'entreprise et d'obtenir successivement d'autres améliorations. Et ce, quasiment en marge de la production quotidienne. Pour cela, il est important de définir des objectifs selon la méthode SMART et de choisir les bons indicateurs pour mesurer la réalisation des objectifs. Vient ensuite la mise en place de boucles de contrôle et l'audit cyclique. Cette dernière garantit que les processus sont adaptés en temps réel aux changements et que les processus de changement en général ne disparaissent pas de l'agenda sans que les potentiels soient exploités.
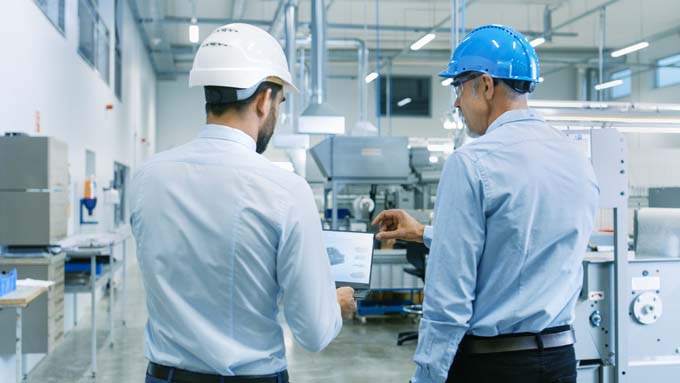
Le MES, base de la Smart Factory
Dans les quatre éléments constitutifs de la production parfaite, le Manufacturing Execution System joue un rôle important en tant que base de la Smart Factory. En effet, si les méthodes Lean pertinentes sont accompagnées de fonctions MES appropriées, c'est la meilleure condition pour bien progresser dans le projet. Comme un MES saisit les données de fabrication en temps réel, il est idéal pour réaliser des temps de réaction courts et des circuits de régulation rapides dans la production. L'exemple cité au début, celui du copeau de métal dans l'huile et de la panne de machine qui en a résulté, montre à quel point il est important de détecter rapidement les dysfonctionnements et de prendre des mesures correctives à temps. La condition préalable est une surveillance permanente de la production - de la situation en termes de délais à la disponibilité du personnel et à la qualité des produits, en passant par l'état des machines et des outils.
Les cinq tâches MES les plus importantes pour réaliser des boucles de contrôle rapides sont les suivantes :
- Surveillance de la production en temps réel : Pour saisir automatiquement les données, les machines et autres périphériques sont directement connectés au MES via des interfaces. Mais une saisie manuelle des données est également possible. La saisie des données d'exploitation fournit un aperçu rapide de la situation actuelle en termes de délais, la saisie des données des machines apporte des informations sur l'état des machines et des installations. L'opérateur voit d'un coup d'œil dans le système si la machine fonctionne (vert) ou non (rouge) et peut réagir sans perte de temps en cas d'arrêt. Pour la planification, les capacités en personnel et la qualification des collaborateurs sont également visibles immédiatement.
- Réaction à court terme aux événements : Une gestion des escalades permet de réagir à court terme aux événements. Outre le dysfonctionnement de la machine déjà mentionné, le dépassement de la valeur limite d'une caractéristique de qualité ou le passage en dessous de cette valeur peut entraîner l'information du responsable qualité. Ou bien le régleur est informé dès que la limite de tolérance d'une valeur de processus n'est pas respectée. En cas d'arrêt de la machine, un MES permet de simuler rapidement les alternatives d'action et de replanifier les commandes par glisser-déposer. Il en va de même pour la planification du personnel.
- Calcul et visualisation d'indicateurs : Sans indicateurs, pas d'amélioration des processus : un Manufacturing Execution System est l'outil idéal pour calculer et visualiser les indicateurs. Il ne peut pas seulement représenter les indicateurs standard comme le taux d'utilisation, l'indice OEE ou le respect des délais. À partir des données saisies, il est également possible de déterminer, par exemple, le rendement du processus et le temps de passage. En outre, les données peuvent être comparées entre elles sur différentes périodes. Chaque niveau de l'entreprise reçoit les informations dont il a besoin.
- Soutien du KVP : La meilleure façon d'éviter les perturbations ou d'améliorer les processus instables est de travailler à l'aide d'un MES, tout à fait dans l'esprit du processus d'amélioration continue (PAC). Le cycle PDCA peut être considérablement accéléré, car les données sont disponibles en un clic. Grâce au niveau de détail plus élevé des informations, il est possible de découvrir davantage de potentiels et de réaliser des améliorations plus rapidement.
- Mise à disposition des données pour les systèmes ERP : Un MES communique les données pertinentes de la production au système ERP supérieur à des intervalles de temps définis - et ferme ainsi la boucle de régulation. La production est régulée à moyen et long terme à l'aide de données telles que l'utilisation effective des capacités. Les informations servent en outre au calcul commercial a posteriori et à la gestion des données de base.
Lorsque les quatre éléments constitutifs de la production parfaite sont mis en œuvre et qu'un Manufacturing Execution System réalise et organise des circuits de régulation rapides, vous avez réussi : vous vous rapprochez de plus en plus des trois dimensions cibles que sont la transparence, la réactivité et la rentabilité de la production. Vous utilisez le potentiel de vos installations de manière optimale, vous connaissez les motifs de panne les plus fréquents et vous savez sur quelle machine vous pouvez vous rabattre lorsqu'un petit copeau de métal dans l'huile de transmission bouleverse votre planification de production.
Auteur :
Jürgen Rieger est membre de la direction de Perfect Production GmbH et auteur du livre spécialisé "Die perfekte Produktion. Manufacturing Excellence in the Smart Factory". Perfect Production GmbH accompagne, en tant que société de conseil, les entreprises de production sur la voie de la production parfaite et fait partie de la Groupe MPDV.