Il retrofit digitale integra i sistemi legacy in flussi di lavoro moderni
Chi non sogna di tanto in tanto di poter digitalizzare i propri macchinari e parchi di impianti senza alcuna eredità, su un sito verde, per così dire? Nella maggior parte dei casi, questo rimane un sogno. In realtà, si tratta soprattutto di convertire una grande varietà di sistemi in flussi di lavoro digitalizzati. Sei scenari applicativi sono esempi di come può essere un retrofit digitale.
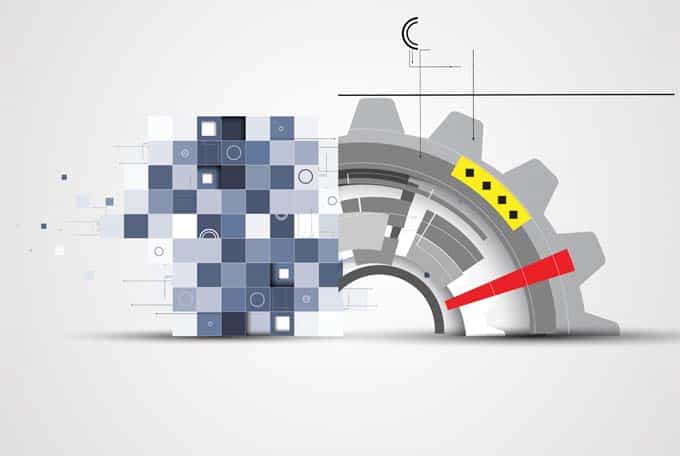
La digitalizzazione è in pieno svolgimento - e nessuno può sfuggirle. Uno dei maggiori ostacoli nell'ambiente industriale è l'integrazione dei vecchi sistemi (retrofit digitale). Questo perché a questi sistemi mancano due importanti prerequisiti: la tecnologia dei sensori per raccogliere i dati e le interfacce dati per inoltrarli. Senza queste capacità, tuttavia, l'ottimizzazione dei tempi di pianificazione e di cambio, l'aumento delle prestazioni e della disponibilità, il miglioramento della tracciabilità della qualità e l'implementazione della manutenzione predittiva non sono possibili.
Retrofit digitale come soluzione
Un retrofit digitale, spesso chiamato anche Retrofit 4.0 in riferimento al termine hype Industry 4.0, consiste quindi nell'equipaggiare i vecchi sistemi con la necessaria tecnologia dei sensori e di controllo - e questo durante il funzionamento continuo, senza interruzioni o tempi morti. La situazione è resa più difficile dal fatto che di solito si tratta di casi individuali speciali. La "taglia unica" è praticamente impossibile con i retrofit. Il retrofit sensoriale-comunicativo richiede quindi un'attenta valutazione e un'analisi di fattibilità per ogni caso. I possibili scenari di applicazione del retrofit digitale sono molto ampi.
Sei scenari di applicazione
LeanBI, uno specialista per applicazioni di scienza dei dati con sede a Berna, descrive sei scenari tipici per l'uso pratico e i potenziali effetti positivi:
- IntralogisticaIl boom del commercio online sta portando a un rapido aumento dei volumi di spedizione e quindi a un elevato utilizzo delle strutture logistiche, che non possono tenere il passo con questa crescita anche a causa della loro struttura (parzialmente) analogica. Tuttavia, gli edifici o i complessi di impianti aggiuntivi non possono essere realizzati così rapidamente come il retrofit delle strutture esistenti. È quindi il modo più veloce, più economico e che fa risparmiare risorse. Inoltre, la vita utile dell'impianto può essere aumentata.
- Linee di assemblaggioPer molti fornitori di prodotti, come i fornitori di automobili o i produttori di biciclette, rispettare i tempi di consegna sta diventando sempre più impegnativo a causa dell'alta domanda e contemporaneamente della crescente diversità di varianti. Nel caso del più piccolo guasto nella catena di produzione, l'intero impianto si ferma, le date di consegna diventano carta straccia e si profilano sanzioni elevate. L'individuazione precoce di possibili guasti attraverso la manutenzione predittiva, che è resa possibile solo dal retrofit, è il fattore chiave per garantire l'affidabilità delle consegne, aumentando la produzione e la soddisfazione del cliente.
- Industria dell'imballaggioLo stesso vale per l'industria dell'imballaggio, dove molte macchine sono collegate in serie. Se una macchina si ferma, si ferma tutta la linea. Con la manutenzione predittiva, sia i malfunzionamenti non pianificati che gli interventi pianificati, come le misure di manutenzione, possono essere ridotti. Inoltre, il retrofit di sistemi esistenti consente l'uso della tecnologia dei sensori per il controllo continuo e automatico della qualità dell'imballaggio di una vasta gamma di prodotti, e quindi per ridurre le percentuali di scarto.
- Produzione di metalloNella fabbricazione di prodotti metallici, come tubi, componenti o parti di carrozzeria, è importante rilevare tempestivamente le variazioni di qualità nel processo. Più la tecnologia dei sensori online è utilizzata, più il controllo del processo può essere progettato in modo reattivo. Inoltre, questo assicura una tracciabilità continua durante l'intero processo. Anche in questo caso, la combinazione della registrazione decentralizzata dei dati e dell'analisi centralizzata dei dati aiuta a ridurre gli scarti.
- Trattamento della superficieUtilizzando sensori aggiuntivi e analisi combinate, è possibile prevedere meglio i tempi di usura degli utensili di lavorazione. Questo ottimizza i processi in diversi modi: i componenti altamente sollecitati nel trattamento delle superfici possono essere utilizzati più a lungo e il consumo di materiale si riduce così come i tempi di inattività, che si riflettono positivamente in un aumento della produttività.
- Produzione elettronica: Retrofit consente di utilizzare metodi di test altamente complessi e assistiti dall'intelligenza artificiale per il rilevamento precoce dei guasti dei componenti nel processo di produzione, aumentando così i tassi di produttività. Aiutano anche a capire meglio e a imparare a risolvere problemi speciali rari.
"Il retrofit digitale è uno dei più importanti prerequisiti e abilitatori di Industria 4.0", spiega Marc Tesch, CEO di LeanBI. "Senza questa tecnologia di modernizzazione sostenibile, molti preziosi e in alcuni casi indispensabili sistemi legacy, impianti di produzione e beni immobili andrebbero persi per il futuro digitale, insieme all'immensa perdita di valore associata e alla rapina di risorse per nuove installazioni costose e che richiedono tempo."
Fonte e ulteriori informazioni: LeanBI