Le Retrofit numérique intègre les anciens systèmes dans des flux de travail modernes
Qui ne rêve pas de temps en temps de pouvoir numériser son parc de machines et d'installations sans avoir à se soucier de l'héritage, pour ainsi dire sur un terrain vierge ? Dans la plupart des cas, cela reste un rêve. Dans la réalité, il s'agit le plus souvent de convertir les systèmes les plus divers en flux de travail numérisés. Six scénarios d'application illustrent à quoi peut ressembler un retrofit numérique.
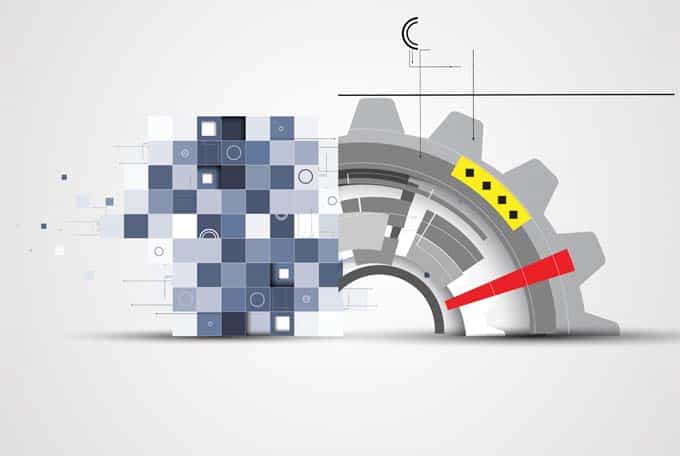
La numérisation bat son plein - et personne ne peut y échapper. L'un des plus grands écueils dans l'environnement industriel est l'intégration d'anciens systèmes (retrofit numérique). En effet, il leur manque surtout deux conditions importantes : les capteurs pour la saisie des données et les interfaces de données pour leur transmission. Or, sans ces capacités, l'optimisation de la planification et des temps de changement, l'augmentation des performances et de la disponibilité, l'amélioration du suivi et de la traçabilité de la qualité ainsi que la mise en œuvre de la maintenance prédictive ne sont pas possibles.
Le rétrofit numérique comme solution
Un retrofit numérique, souvent appelé Retrofit 4.0 en référence au terme à la mode Industrie 4.0, consiste donc à équiper les anciens systèmes de la technique de capteurs et de commande nécessaire à cet effet - et ce en cours de fonctionnement, sans break ni downtime. La situation est d'autant plus difficile qu'il s'agit généralement de cas particuliers. Le "one size fits all" est pratiquement exclu pour le retrofit. Le rétrofit sensoriel et communicationnel nécessite donc à chaque fois un inventaire et une analyse de faisabilité minutieux et adapté à l'application. Les scénarios d'application possibles pour le retrofit numérique sont très variés.
Six scénarios d'application
LeanBI, un spécialiste des applications de science des données dont le siège est à Berne, décrit six scénarios typiques d'utilisation pratique et les effets positifs potentiels :
- IntralogistiqueLe commerce en ligne en plein essor entraîne une augmentation rapide des volumes d'expédition et donc une forte utilisation des installations logistiques qui ne peuvent pas suivre le rythme de cette croissance, notamment en raison de leur structure (partiellement) analogique. Des bâtiments ou des complexes d'installations supplémentaires ne sont toutefois pas réalisables aussi rapidement qu'un retrofit des installations existantes. Il s'agit donc d'une solution à la fois plus rapide, plus économique et plus respectueuse des ressources. De plus, cela permet d'augmenter la durée de vie de l'installation.
- Lignes de montagePour de nombreux fournisseurs de produits, comme les sous-traitants automobiles ou les fabricants de vélos, le respect des délais de livraison devient de plus en plus difficile en raison de la forte demande et de la multiplication des variantes. La moindre défaillance dans la chaîne de production entraîne l'arrêt de l'ensemble de l'installation, les délais de livraison ne sont plus respectés et de lourdes pénalités peuvent être appliquées. La détection précoce des pannes éventuelles grâce à la maintenance prédictive, rendue possible par le retrofit, est le facteur clé pour garantir le respect des délais de livraison, augmenter les performances de production et satisfaire les clients.
- Industrie de l'emballageIl en va de même dans l'industrie de l'emballage, où de nombreuses machines sont montées en série. Si une machine s'arrête, c'est toute la ligne qui s'arrête. La maintenance prédictive permet de réduire aussi bien les pannes imprévues que les interventions planifiées, comme par exemple les mesures de maintenance. De plus, le retrofit d'installations existantes permet d'utiliser des capteurs pour contrôler en permanence et de manière automatisée la qualité de l'emballage des produits les plus divers, et donc de réduire les taux de rebut.
- Production de métalLors de la fabrication de produits métalliques, tels que des tubes, des composants ou des pièces de carrosserie, il est important de détecter à temps les variations de qualité du processus. Plus on utilise de capteurs en ligne, plus le contrôle du processus peut être réactif. De plus, cela permet d'assurer une traçabilité continue tout au long du processus. Ici aussi, la combinaison d'une collecte de données décentralisée et d'une analyse de données centralisée permet de réduire les rebuts.
- Traitement de surfaceL'utilisation de capteurs supplémentaires et d'analyses combinées permet de mieux prévoir les temps d'usure des outils d'usinage. Cela permet d'optimiser les processus à plusieurs niveaux : les composants fortement sollicités lors du traitement de surface peuvent être utilisés plus longtemps et la consommation de matériaux est réduite, tout comme les temps d'arrêt, ce qui se traduit par une productivité accrue.
- Production électroniqueRetrofit : des méthodes de contrôle très complexes, assistées par l'IA, peuvent être utilisées pour la détection précoce des défaillances de composants dans le processus de production, ce qui permet d'augmenter les taux de productivité. Elles permettent également de mieux comprendre les problèmes spéciaux rares et d'apprendre à les résoudre.
"La modernisation numérique est l'une des conditions préalables les plus importantes et ouvre la voie à l'industrie 4.0", explique Marc Tesch, CEO de LeanBI. "Sans cette technologie de modernisation durable, de nombreux systèmes patrimoniaux, sites de production et biens immobiliers précieux et parfois indispensables seraient perdus pour l'avenir numérique, avec les immenses pertes de valeur que cela implique et le pillage des ressources pour de nouvelles installations coûteuses et chronophages".
Source et informations complémentaires : LeanBI