A new AI model could streamline processes in a robot warehouse
The future belongs to automated warehouse handling: robots pick goods from shelves and assist with order picking. But where hundreds of robots are whizzing through warehouses, traffic problems can certainly arise. Researchers at the Massachusetts Institute of Technology MIT have addressed this problem. Once again, the solution lies in AI.
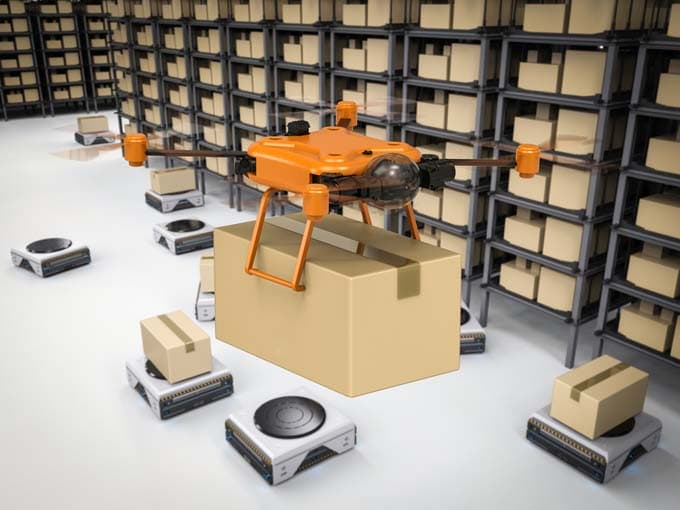
The scene is a warehouse somewhere in the world: robots scurry across the floor and pick up items, which they then hand over to human employees for packing and shipping. In many industries, from e-commerce to automotive production, warehouses with hundreds of robots are increasingly becoming part of the supply chain. The problem is that when 800 robots are on the move at the same time to efficiently deliver goods to their destinations, the risk of collisions increases. Even the best path-finding algorithms struggle to keep up with the fast pace of e-commerce or production. In a way, the robots are like cars that have to find their way in a crowded city center.
Intelligent traffic planning in the robot warehouse
A group of MIT researchers are already using AI to alleviate traffic congestion. They have adopted ideas from this field to tackle the problem of robot traffic in warehouses. To this end, they have developed a deep learning model that encodes important information about the warehouse. This includes information about robots, planned paths, tasks and obstacles. The model can be used to predict which areas of the warehouse should best be relieved to improve overall efficiency. The technique divides the warehouse robots into groups to unload them faster using traditional robot coordination algorithms. This allows the robots to be relieved almost four times faster than when using a strong random search method. Specifically, the new neural network architecture considers smaller groups of robots at the same time. In a warehouse with 800 robots, for example, the network could divide the warehouse into smaller groups of 40 robots each. It then predicts which group has the greatest potential to improve the overall solution when a search-based solver is used to coordinate the path to be traveled by the robots in that group. In an iterative process, the overall algorithm selects the most promising group of robots with the neural network, offloads the group with the search-based solver, then selects the next promising group with the neural network, and so on.
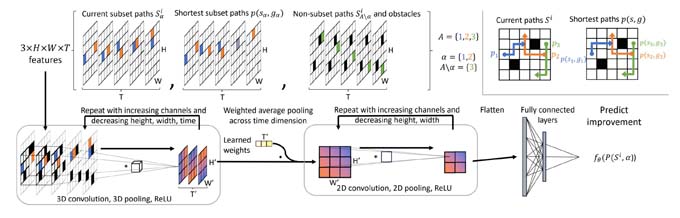
Consideration of relationships
In addition, the neural network records the complex relationships between the individual robots. Even if one robot is initially far away from another, their paths can still cross while traveling through the robot warehouse. The technology also streamlines the calculation as the constraints only need to be coded once instead of repeating the process for each sub-problem. In a warehouse with 800 robots, 40 robots can be relieved by setting the other 760 as constraints. Other approaches require all 800 robots to be considered in each iteration per group. Instead, the 800 robots only need to be considered once across all groups in each iteration. This deep learning approach could be used not only for streamlining warehouse operations, but also for other complex planning tasks such as designing computer chips or laying pipelines in large buildings.
"We have developed a new neural network architecture suitable for real-time operations at the scale and complexity of these warehouses. It is able to encode hundreds of robots in terms of their trajectories, origins, destinations, and relationships to other robots in an efficient way that reuses computations across groups of robots," summarizes Cathy Wu, Gilbert W. Winslow Career Development Assistant Professor in Civil and Environmental Engineering (CEE) and a member of the Laboratory for Information and Decision Systems (LIDS) and the Institute for Data, Systems, and Society (IDSS). Cathy Wu is the lead author of an article on this technique, and is assisted by Zhongxia Yan, a PhD student in electrical and computer engineering.
Source: techexplore.com